Vertical Powder Coating Line for Aluminium Profiles up to 7m
-
Client:SUYS Czechia s.r.o.
-
Year of implementation:2025
-
Location:Velká Bíteš - Košíkov (CZ)
-
Technical specifications:
- Max Product Dimensions:
L 7000 x H 300 x W 300 mm
- Max Product Weight: 75 kg
- Line throughput: 540 parts per hour
- Qualicoat Certification
- Automatic platform loading station
- Nine-stage continuous pre-treatment
Controlled dosing and continuous monitoring
via Bonderite E-CO Flex system - Drying oven
- Curing oven
- Automatic unloading station
- Laser hook cleaning
- Continuous wastewater treatment unit
- Dual demineralisation unit with continuous regeneration
- Max Product Dimensions:
-
Client:SUYS Czechia s.r.o.
-
Year of implementation:2025
-
Location:Velká Bíteš - Košíkov (CZ)
-
Technical specifications:
- Max Product Dimensions:
L 7000 x H 300 x W 300 mm
- Max Product Weight: 75 kg
- Line throughput: 540 parts per hour
- Qualicoat Certification
- Automatic platform loading station
- Nine-stage continuous pre-treatment
Controlled dosing and continuous monitoring via Bonderite E-CO Flex system - Drying oven
- Curing oven
- Automatic unloading station
- Laser hook cleaning
- Continuous wastewater treatment unit
- Dual demineralisation unit with continuous regeneration
- Max Product Dimensions:
Technical Description of the Implementation
Automation of Powder Coating Processes for 7-Metre Aluminium Profiles in Shading Solutions Manufacturing
For SUYS Czechia s.r.o., we designed and installed a vertical powder coating line capable of processing parts up to 7 metres in length. But it’s not just about height – this is the first automatic powder coating line of its kind in the Czech Republic. It features a range of smart solutions that allowed the manufacturer of shading solutions to transition to fully automated production aligned with Industry 4.0 principles. The combination of automation, energy efficiency, and a strong focus on quality is packed into a compact footprint—yet the line can handle up to 540 parts per hour. How did we achieve that? And which technologies made it possible?
Maximum Output in Minimal Space
While designing the line, we were given a clear brief: achieve industrial-scale powder coating performance within the smallest possible footprint. That’s why we opted for a vertical solution. Our custom-designed system is capable of coating aluminium profiles up to 7 metres in length – while occupying just 32 × 26 metres of floor space. This compact layout also required an intelligent approach to part handling. Components are hung in a horizontal position and gradually transition to vertical via an angled loading platform. Suspended from an overhead conveyor, they pass through the line and are automatically rotated back to a horizontal position at the unloading station, ready for easy packing and dispatch. The result is seamless material flow, automated part handling, and maximum efficiency—even in a limited space.
Automated Chemical Dosing and Pre-treatment Monitoring
The line includes a nine-stage continuous chemical pre-treatment process, managed by the Bonderite E-CO Flex system from Henkel. This intelligent system maintains stable bath quality through automatic dosing based on monitored chemical parameters, which are regularly checked and adjusted by operators according to daily laboratory test results. The result is consistent surface pre-treatment quality without fluctuations. Operators simply set the target values and ensure the pumps are supplied with chemicals – the rest is handled automatically by the line.
Thanks to these features, obtaining Qualicoat certification was significantly easier.
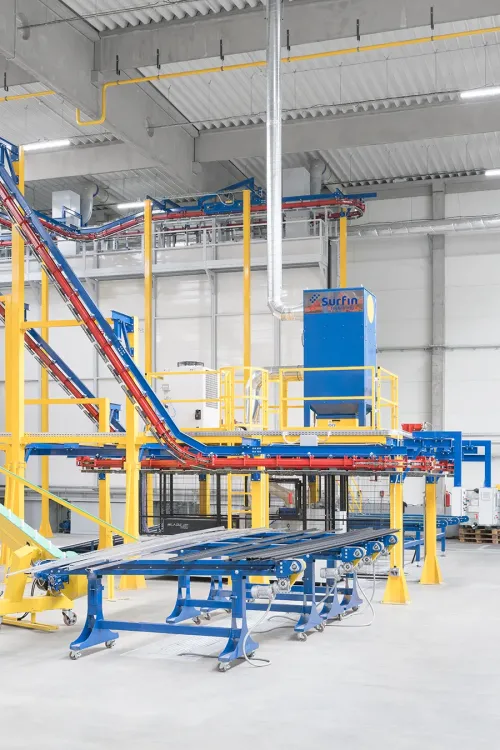
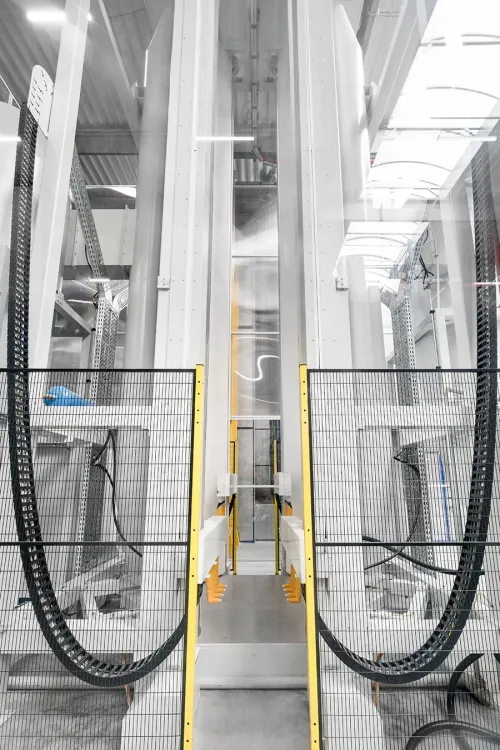
Powder Coating Process Designed for Precision and Efficiency
One of the key requirements for the automatic line was to handle the coating of 7-metre-long parts without compromising on precision or output consistency. To meet this challenge, we relied on modern powder coating technologies. We implemented a pair of vertical-axis reciprocators, which ensure full coverage along the entire part length. Behind them, recovery belts collect any excess powder for reuse – reducing both material waste and operating costs. The entire coating station is housed in a controlled environment that minimises external contamination and guarantees consistent coating results.
Eco-Friendly and Energy-Efficient Coating
The latest coating lines built on Industry 4.0 principles stand out not only for their automation and speed but also for their focus on sustainability. Our solution for SUYS is no exception. The aluminium profile coating line uses a two-stage heat recovery system – reusing heat from the curing oven as well as from the hot processed parts to warm the drying oven. This nearly eliminates the need for external heating, and during winter months, the remaining heat is also used to warm the air handling unit. The heating system is fully electric, and the line can also be connected to a photovoltaic power source. With these technologies, the line enables environmentally responsible production and energy-efficient coating – without compromise.
Laser Hook Cleaning and Continuous Water Recycling
Conventional coating lines require hooks to be removed and manually stripped of paint – resulting in time losses, wear, and increased inventory demands. Our solution takes a more elegant approach: laser cleaning directly on the conveyor. Hooks are cleaned automatically during operation – without interruption and without operator input. This ensures a smooth, continuous workflow with no unnecessary downtime. We applied the same philosophy to water management. An integrated treatment system with continuous regeneration not only purifies the water but also produces demineralised water as needed. The result is stable, low-maintenance operation that contributes to more sustainable manufacturing.