Automatic wet coating line with robotic application
-
Client:Alcadrain s.r.o.
-
Year of implementation:2024
-
Location:Břeclav (CZ)
-
Technical specification:
- Max Product Dimensions:
- 500 x 500 mm
- 2K application technology
- Coating robot IRB 52
- Handling robot IRB 1600
- Flame treatment station
- Ionization station
- ESCO control system
- Floor conveyor
- Drying oven
-
Client:Alcadrain s.r.o.
-
Year of implementation:2024
-
Location:Břeclav (CZ)
-
Technical specification:
- Max Product Dimensions:
- 500 x 500 mm
- 2K application technology/li>
- Coating robot IRB 52
- Handling robot IRB 1600
- Flame treatment station
- Ionization station
- ESCO control system
- Floor conveyor
- Drying oven
Technical Description of the Implementation
Increasing Production Capacity for Alcadrain s.r.o.
Alcadrain is a leading manufacturer of sanitary equipment in the Czech market. Since its establishment, the company has experienced continuous growth in order volumes. This was one of the key reasons behind the decision to invest in a new automatic wet coating line with robotic paint application. This advanced coating line now ensures a high-quality finish for Alcadrain’s plastic flush buttons.
Robotic Coating Line Increased Production Capacity and Reduced Liquid Coating Consumption
The automated robotic coating line with flame treatment has significantly boosted coating capacity. The integration of robotic application into the manufacturing process led to a reduction in coating material consumption. The line has thus contributed to production optimization while ensuring precise and consistent surface finishing of plastic parts. Thanks to advanced wet coating technology, the system delivers uniform paint application and high surface durability.
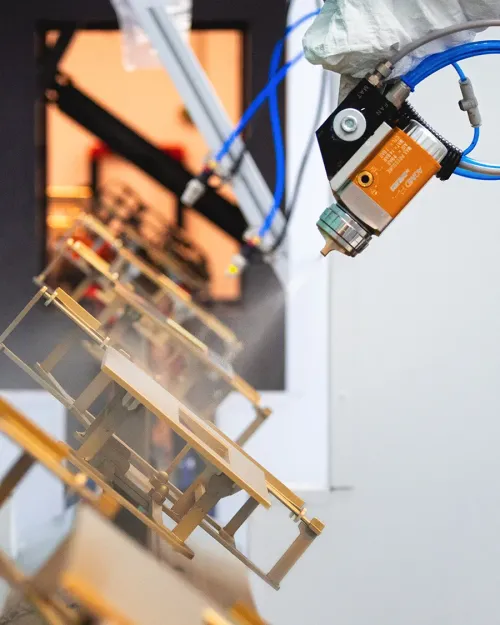
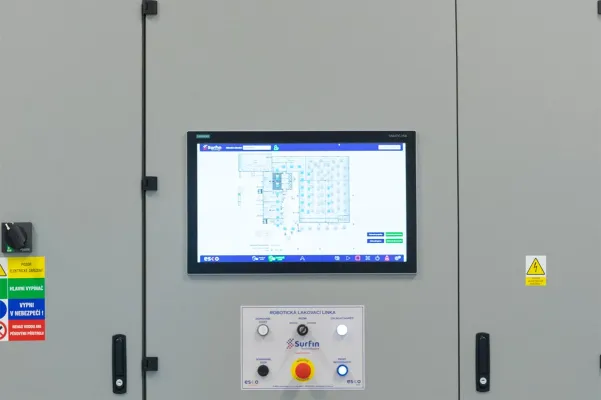
High-Quality Wet Coating for a Flawless Appearance and Functionality
Thanks to automation and process consistency, it is easy to maintain the high-quality standards required for coatings - an essential aspect of products we interact with multiple times a day in our homes. These components are not just functional parts of sanitary equipment but often serve as striking design elements within interior spaces.
ESCO Control System for an Efficient Coating Process
The entire coating process is controlled by our advanced ESCO control system, which enables automatic parameter adjustments of the coating line and data collection for production optimisation. If an issue arises on the line, it is immediately reported to the operator and logged for detailed analysis.
Let’s take a detailed look at the coating process.
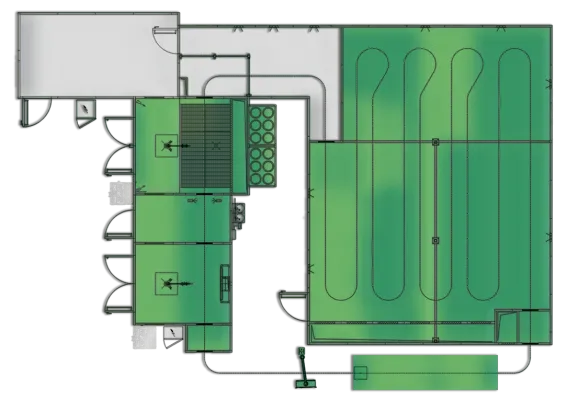
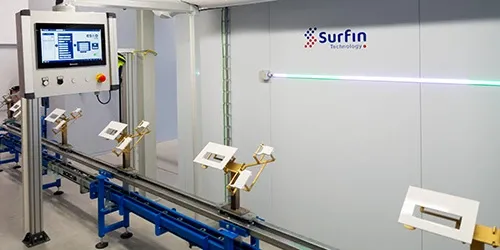
Efficient Loading
for a Smooth Process
Thanks to custom-made holders, both the main component and individual flush buttons can be securely fixed, optimising the coating process.
This hanging technology ensures the precise positioning of parts during wet coating, minimising deviations and enhancing surface quality.
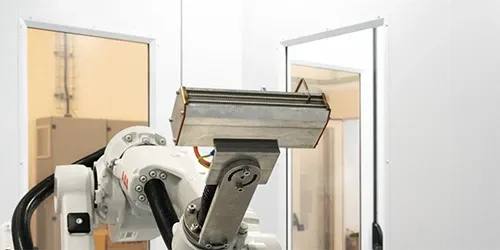
Robotic
Pre-Treatment of Parts
The flame treatment robotic station heats the surface of the coated part within seconds, creating a uniform layer.
This prevents the occurrence of surface defects.
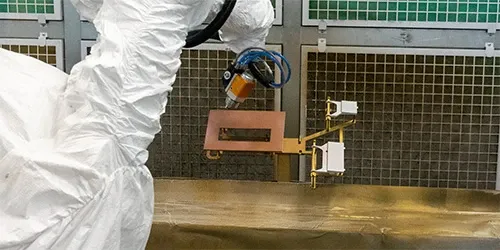
Complete
Robotic Coating
The liquid coating is applied in a fully automated robotic coating station, ensuring complete coverage of all components, including the sides and inner surfaces of button areas.
This results in greater precision, reduced paint consumption, and consistent surface quality.
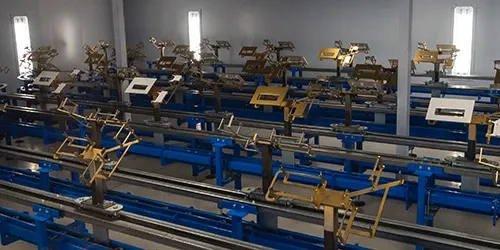
Drying Oven
with Floor Conveyor
Once the coating process is complete, the parts are transported via a floor conveyor to the drying oven, where the paint gradually dries.
The components are then smoothly moved to the unloading area, where they are removed and replaced with new parts for coating.
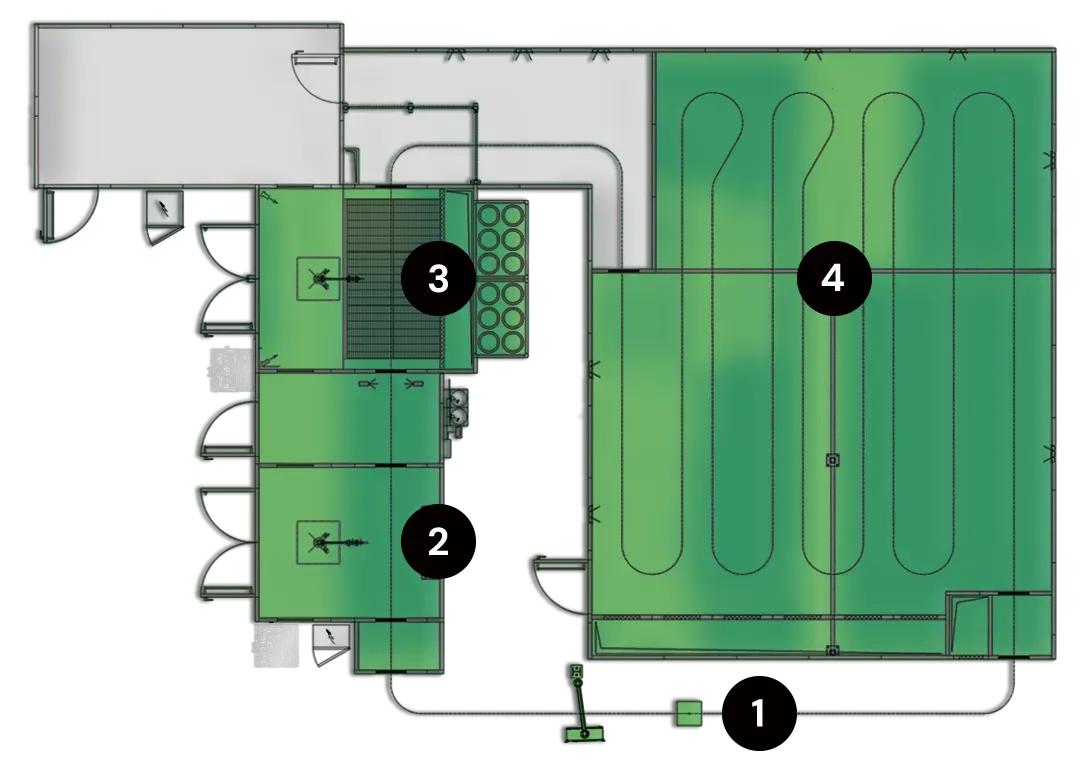
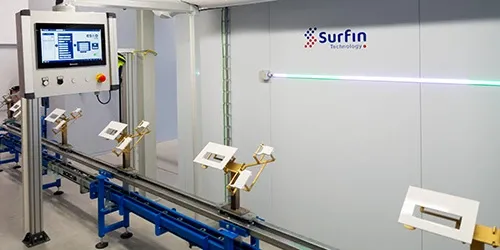
Efficient Loading
for a Smooth Process
Thanks to custom-made holders, both the main component and individual flush buttons can be securely fixed, optimising the coating process.
This hanging technology ensures the precise positioning of parts during wet coating, minimising deviations and enhancing surface quality.
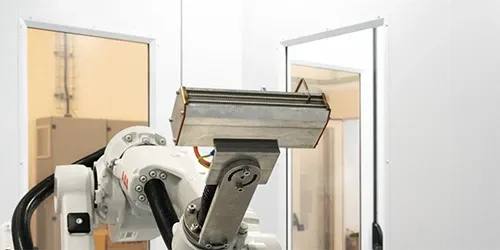
Robotic
Pre-Treatment of Parts
The flame treatment robotic station heats the surface of the coated part within seconds, creating a uniform layer.
This prevents the occurrence of surface defects.
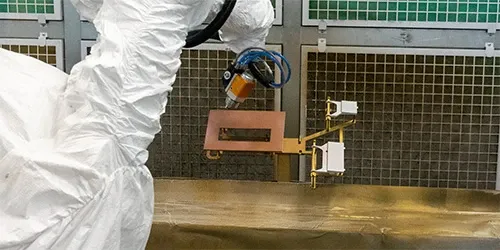
Complete
Robotic Coating
The liquid coating is applied in a fully automated robotic coating station, ensuring complete coverage of all components, including the sides and inner surfaces of button areas.
This results in greater precision, reduced paint consumption, and consistent surface quality.
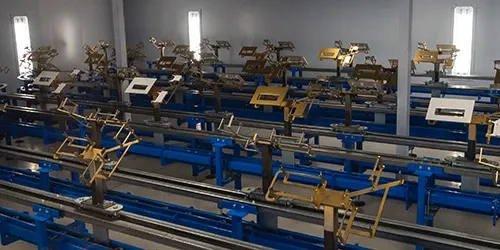
Drying Oven
with Floor Conveyor
Once the coating process is complete, the parts are transported via a floor conveyor to the drying oven, where the paint gradually dries.
The components are then smoothly moved to the unloading area, where they are removed and replaced with new parts for coating.